Meeting the Customized Demands of Gasket Cutting
The gasket industry is moving towards customization, driven by diverse industrial needs. To meet these requirements, businesses are shifting to advanced cutting solutions. Let’s explore the various types of gasket cutting machines and how to choose the best one for your needs.
Common Types of Gasket Cutting Machines
Laser Cutting Machines
Ideal for thin, non-reflective materials but can damage heat-sensitive gaskets like non-asbestos or rubber due to thermal cutting.
Water Jet Cutting Machines
Suitable for cutting thick materials but requires significant maintenance and has higher operating costs.
Oscillating Knife Cutting Machines
A versatile choice for precise, clean cuts on a wide range of non-metallic materials without thermal damage.
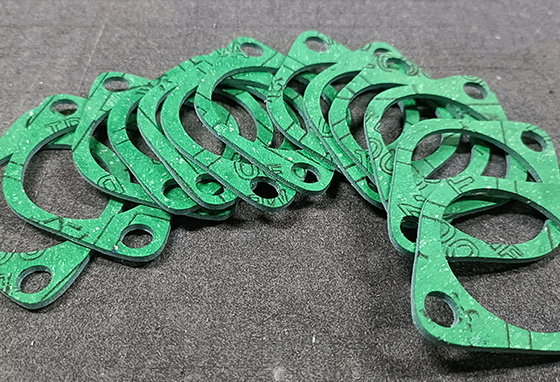
Meeting the Customized Demands of Gasket Cutting
How to Choose a Gasket Cutting Machine?
Material Compatibility:
Ensure the machine supports your material type and thickness (e.g., rubber, asbestos, PTFE).
Cutting Precision:
Look for features like adjustable speed, depth, and compensation settings.
Cost Efficiency:
Consider the maintenance, operational costs, and efficiency.
Customizability:
Machines like oscillating knife cutters offer flexible production for various shapes and sizes.
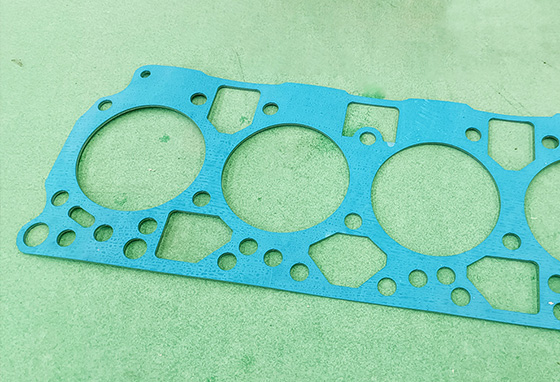
How to Choose a Gasket Cutting Machine
Oscillating Knife Gasket Cutting Machines
What is an Oscillating Knife Gasket Cutting Machine?
An oscillating knife cutting machine uses rapid up-and-down blade motions to precisely cut materials without heat or damage. It eliminates the need for molds, making it a top choice for customized gasket production.
Applications
Oscillating knife gasket cutting machines are used to cut a wide range of gasket materials with precision. Common applications include:
- Sealing and Insulation: Cutting rubber, silicone, and non-asbestos gaskets.
- Automotive: Producing gaskets for engines, exhausts, and HVAC systems.
- Aerospace: Crafting lightweight, durable gaskets.
- Electronics: Making insulating gaskets for electronic devices.
Features
- Precise Cutting: Delivers clean and smooth edges, perfect for complex designs.
- Versatile: Cuts rubber, PTFE, non-asbestos sheets, and more.
- No Heat Damage: Cold cutting ensures no burning or warping.
- Flexible Production: No need for molds, great for custom and small-batch orders.
- Eco-Friendly: Dust-free, no smoke or harmful fumes.
- Easy to Use: Simple tool changes and user-friendly software.
- Durable: Low maintenance, with easy blade replacement.
What is an Oscillating Knife Gasket Cutting Machine
Tools Used in Oscillating Knife Machines
- 400W Electric Oscillating Tool
Cuts hard materials like PTFE and non-asbestos gaskets. - Pneumatic Oscillating Tool
Ideal for soft materials like rubber and silicone sheets. - High-Speed Rotary Milling Cutter
Used for rigid materials like fiberglass sheets. - High-Frequency Oscillating Knife
Great for medium-hard materials like felt and cork.
These tools make the machine versatile for cutting different materials with precision.
Different Blade Shapes for Oscillating Knife Cutting Machines
Oscillating knife cutting machines use different blade shapes to handle materials of various thicknesses, hardness levels, and cutting patterns.
- Different Blade Lengths for Material Thickness
Longer blades are used for cutting thicker materials, ensuring the blade penetrates fully and produces clean edges. - Varied Blade Shapes for Specific Cuts
Pointed Blades (26°, 16°, 10°): Ideal for detailed cuts, like small circles, ensuring precision.
Straight-Edge Blades: Used for testing and achieving perfect circular cuts with smooth edges. - Different Blade Widths for Accuracy
Narrow Tips: Suitable for thin materials and tiny circular cuts.
Wider Base (1-2mm): Reduces overcutting by keeping the blade width consistent during cutting. - Blade Thickness for Material Hardness
Blades come in 0.63mm, 1mm, and 1.5mm thicknesses. Thicker blades are used for harder or denser materials, providing stability and durability during the cutting process.

Different Blade Shapes for Oscillating Knife Cutting Machines
These blade variations allow the machine to adapt to diverse materials and cutting tasks, delivering precise and efficient results for different applications.
Features and Applications of Different Cutting Tools
400W High-Power Electric Oscillating Tool
- Features: Driven by a 400W servo motor, with a 5mm amplitude and 4000 vibrations per minute. Powerful and stable.
- Applications: Ideal for cutting extremely hard and thick materials like graphite-reinforced gaskets, PTFE gaskets, and high-pressure non-asbestos gaskets.
Pneumatic Oscillating Tool
- Features: Powered by high-pressure gas (≥0.6MPA), with an 8mm amplitude and 8000 vibrations per minute.
- Applications: Suitable for medium-density and medium-thickness materials like rubber sheets, silicone sheets, and cork boards.
High-Speed Electric Oscillating Tool
- Features: Runs on a 120W brushless DC motor, with a 1-1.5mm amplitude and a high vibration frequency of 15,000 times per minute. Fast and precise.
- Applications: Best for thin, medium-density materials such as 1-5mm rubber sheets, providing smooth, burr-free cutting edges.
High-Speed Rotary Milling Cutter
- Features: Power ranges from 800W to 1500W, with a rotation speed of 40,000 RPM. Designed for tougher materials.
- Applications: Perfect for cutting hard materials like epoxy boards, MDF, and acrylic sheets, significantly expanding the machine’s capabilities.
These tools allow oscillating knife cutting machines to handle a wide variety of materials efficiently and with precision. Each tool is designed to meet specific cutting needs, ensuring flexibility in production.

Features and Applications of Different Cutting Tools
Installing and Using Oscillating Cutting Tools
Blade Installation
Insert the blade fully into the blade holder and tighten the screws securely.
Ensure the sharp edge of the blade faces the side of the fixed screw. This centers the blade tip for precise cutting.
Tool Placement
Insert the tool into the tool holder and tighten the bolt clockwise to secure it firmly.
When the W-axis is at the zero position, the blade edge should point toward the machine’s X+ direction. This confirms correct installation.
SP Operation Numbers
Use the correct SP number for the tool’s specific function (e.g., SP4 for electric oscillating tools, SP5 for milling tools).
Cutting Depth Settings
Adjust the cutting depth and lifting height in the SP operation settings to match the material thickness.
For tools with large amplitudes (3-8mm), set the depth while the tool is oscillating to ensure optimal results.
Cutting Speed
Set speeds based on the material’s thickness and hardness.
Adjust straight-line speed, acceleration, curve speed, and small-circle speed.
For harder materials, reduce the tool’s descending speed to prevent blade damage and achieve clean, burr-free edges.
These steps ensure accurate, efficient cutting while protecting the blade and delivering high-quality results.